The transmission line connection point is a major weak point of inline operation. In the operation of often heat burned, thus causing power outages. The analysis of the wire connection point heating problem, and timely adoption of appropriate preventive measures, will effectively avoid the wire connection point overheating. This causes the wire connection point to burn off the accident. Analyze the causes of wire connection point heating, and understand the theoretical basis for the temperature rise of high-voltage lines. At the same time, mastering the prevention and solution measures to deal with the connection point heating problem, to ensure the safe and reliable operation of the line has practical significance.
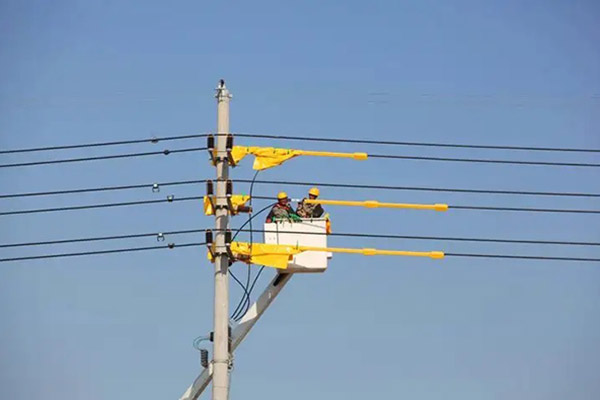
Situation one: vibration of the wire in the wind during operation makes the equipment bolt lose and generates a large temperature rise.
Situation two: due to the line construction process, the installation of the tension-resistant line clip bolt torque is not enough and the contact surface of the connecting parts is not tight, resulting in the contact resistance of the equipment clip increases, generating heat phenomenon.
Situation three: high-load operation of high-voltage transmission lines, after a long period of operation, resulting in connecting parts (including line clip joints, crimp joints, etc.) temperature is significantly higher than its normal operating temperature.
A. The specific form of the conductor conductive heating of the tension-resistant tower
1. Conductor diversion heating parts
Transmission lines with tension tower wire diversion heating parts usually have: connecting the diversion and trench clamps, using bolts connected to the tension line clamps, tension line body heating.
2. Defect judgment method
According to the “Application Guidelines for Infrared Diagnostic Techniques for Powered Equipment” (DL/T664-2016), the judgment methods are divided into six main types.
Ⅰ surface temperature judgment method.
Ⅱ relative temperature difference judgment method.
Ⅲ Similar comparison judgment method.
Ⅳ Similar comparison judgment method.
Ⅴ comprehensive analysis judgment method.
Ⅵ real-time analysis and judgment method.
3. Relative temperature difference judgment method
For current heating equipment, if the thermal state of the inflow part of the equipment is found to be abnormal, the temperature should be measured accurately according to the correct operation of the infrared thermometer, and the relative temperature difference value should be calculated to determine the nature of the equipment defect.
Relative temperature difference: the temperature difference between the two corresponding measurement points and the percentage of the temperature rise of the hotter point.
When the temperature rise value of the hot spot is less than 10K, it is not appropriate to determine the nature of equipment defects according to the provisions of Table 1. For the small load rate, the temperature rise is small but the relative temperature difference between the equipment. If there are conditions to change the load rate, the load current can be increased after the retest to determine the nature of equipment defects. When such retesting is not possible, can be provisionally set as a general defect, and pay attention to monitoring.
4. Infrared thermometer temperature measurement example
The use of infrared thermometer chromatographic imaging can be clearly observed in the diversion of defective parts and the corresponding temperature. The highest test temperature of the heat-resistant wire clamp parts of 127 ℃, the normal corresponding point temperature of 38 ℃, the environmental reference body temperature of 30 ℃, and the relative temperature difference of 91.7%, is a major defect.
B. The main reason for the diversion line heating analysis
1. the cause of poor connection of the diversion connector
Taking into account that the diversion heating fault generally occurs only in the tension-resistant diversion of a phase, the other two phases did not appear in such a situation. Therefore, the line operating under a large load only accelerates the occurrence of the fault and is not the main factor causing the heating. Through the analysis of 220kVxxx line 51# pole C phase heating parts found that this section of the diversion of the parallel trench line clip bolt loosening defects. Loose bolts lead to trenching wire clips with poor contact with the surface of the wire, as the load increases there is a sharp increase in temperature and produces a vicious cycle of wire clip defects aggravated. The inspection of other heat-generating devices found that the connection is poorly connected to the main cause of the diversion of heat.
Caused by the poor connection of the diversion connector is mainly due to: serious oxidation of wires and fixtures, the role of mechanical forces, construction techniques are not strict, spring aging 4, its specific circumstances are as follows.
(1) the line runs for too long, because of rain, snow, fog, harmful gases and acid, alkali, salt, and other corrosive dust pollution and erosion, resulting in the connection of the gold fixture connection oxidation, etc.
(2) the diversion line itself is not subject to tension, under the action of mechanical forces such as wind or vibration, as well as the periodic loading of the line and the periodic changes in ambient temperature, so that the connection slack.
(3) The installation construction is not strict and does not meet the process requirements. Such as the contact surface of the connection is not clean oxidation layer and other dirt, in the maintenance, installation of the connection is not added spring washers, the nut tightening degree is not enough, the connection is not bent, etc. will reduce the quality of the connection. Connections within the wire are not equal to the diameter of the contact area is reduced.
(4) long-term operation, caused by the aging of the spring, will also make the connection slack connection, resulting in heat.
2. The main mechanism of the tension-resistant towers is lead wire heating
Tension-resistant tower’s lead line heating is a current-causing thermal effect defect. When the current-carrying conductor is in operation, due to the existence of certain resistance, there is bound to be part of the electrical energy loss, so that the temperature of the current-carrying conductor rises. The resulting heat power is P = Kf I2 R where P is the heat power (w). I am the current strength (A). R is the DC resistance of the current-carrying conductor (Ω). Kf is the additional loss coefficient, indicating that in the AC circuit and the skin effect and proximity effect when the resistance increases the coefficient.
(1) the size of the contact resistance and the relationship between the temperature, and the size of the contact resistance Rj can be expressed by the empirical formula Rj = (K / Fn) × 10-3 formula, F is the contact pressure (Kg). k is the coefficient related to the contact material and contact surface shape, taken between 0.07-0.1. n is dependent on the contact form of the index (in 0.5–0.75). 0.75).
(2) The relationship between contact resistance Rj and temperature Rj = Rjo (1 2/3 × a × t) In the formula, Rjo is the contact resistance value (Ω) at a temperature of 0 °C. A is the resistance temperature coefficient of the contact metal (I / ℃). T is the operating temperature (℃).
Through the above analysis, various connections in the transmission line under ideal conditions, the contact resistance is lower than the resistance of the connected wire parts, the loss of heat generation in the connected parts will not be higher than the adjacent current-carrying conductor heat generation. Only when the contact resistance is abnormal and the current passes through, it will produce heating defects. And the contact resistance varies with the temperature. When the temperature of the contact part reaches 70℃ or more, the metal oxidation starts to be intense, and the oxidation generation makes the contact resistance increase more rapidly, even causing a vicious circle, and the contact part will further overheat, resulting in burnout.
To reduce the temperature of the lead connection device, we must reduce the heat generation power. According to the formula of heat power, reducing the strength of the current and reducing the contact resistance can be achieved to reduce the heat power. The line where the current failure occurs is a high load line. Therefore, reducing the current strength is not easy to achieve. An easier way is to reduce the equivalent resistance of the current draw.
C. The solution to the tension resistance of the diversion of the heating method
1. the use of the equipotential operation method to tighten the line clip bolt
The use of equipotential operation method to tighten the line clip bolt, this method is applicable as the bolt is loose and the bolt is intact with heart defects.
2. Installation of wire shunt
Installation of wire shunt, this method is applicable to the bolt fastening method can not deal with the defects and the lead wire body heating defects.
Analysis of the principle: according to the main mechanism of the tension-resistant tower diversion line heating combined with the principle of parallel circuit shunt, take a new branch (wire shunt) in parallel. The contact resistance of the new branch and the wire and the resistance of the branch itself is much smaller than the contact resistance of the heating part so that most of the line current through this new branch achieves the reduction of the current through the heating part, to reduce the temperature of the heating part.
3. The production of wire shunt and installation with electricity
(1) wire shunt structure
The whole set of wire shunts mainly consists of two parts, two-wire connectors and wire parts (according to the actual need to intercept). The wire connector is the main apparatus to achieve the short connection of the heating part, through a section of wire to connect the two-wire connectors.
(2) the construction method of installing the wire shunt with electricity
First, the ground staff assembles the wire shunt, tower staff with insulation transfer rope to the tower work position, good safety measures. Ground staff with the transferring rope and then the insulated operating rod to the tower operator. With the operating rod in place, the ground staff with the transferring rope tied wire shunt pulled to work (work for the diversion of the ends of the fault line clamps), should pay special attention to the safety distance. Tower staff uses the operating rod operation, with the ground staff screw knob parts to make the connector and the diversion line fixed solid.
4. with power to install the wire shunt post-maintenance
Installing the wire shunt with electricity can quickly solve the problem of tension resistance diversion heat, but is a temporary treatment method. As a result of the installation under live operation, the staff must use insulated operating rods, which reduces the tightness of the connection between the wire connector and the lead wire. After a long period of operation, the wire connector and the connection part of the lead wire will be loose, the wire shunt can not be normal to the load current of the lead wire shunt, which will cause the heating part to heat up again. It is recommended that the line has the opportunity to blackout, permanent treatment of the heating parts. Strengthen the monitoring and infrared temperature measurement of the towers where the conductor shunt is installed, especially in the high load state of the line.