Hydrocarbon-resistant cables are essential in environments exposed to various hydrocarbon substances like oils, fuels, and solvents. Designed to withstand corrosive effects, these cables ensure reliability and safety, especially in industries where exposure to hydrocarbons is frequent. This article will explore the unique features of hydrocarbon-resistant cables, their key applications, and why they are crucial in sectors that deal with oil and chemical exposure.
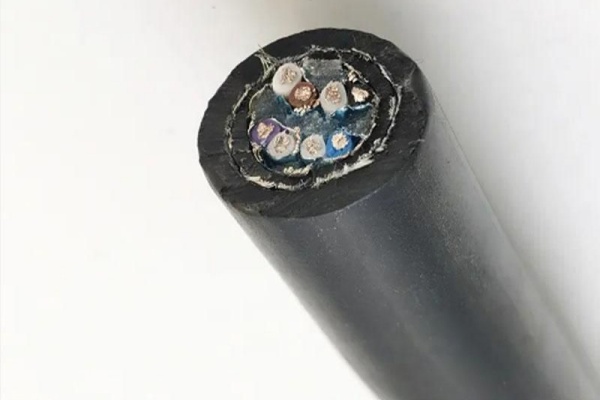
Understanding Hydrocarbon Resistance in Cables
Hydrocarbon resistance in cables refers to the ability to withstand degradation when exposed to hydrocarbons. Hydrocarbons, organic compounds consisting primarily of hydrogen and carbon atoms, are found in petroleum, natural gas, and various industrial chemicals. Over time, these compounds can deteriorate standard cable materials, leading to loss of flexibility, cracking, or complete failure.
To combat these effects, hydrocarbon-resistant cables are manufactured with specially formulated materials, such as polyethylene (PE), fluoropolymer (such as Teflon), and polyurethane (PUR), designed to resist hydrocarbon penetration. These materials not only provide resistance to oils and fuels but also ensure that the cable maintains its electrical and mechanical properties under prolonged exposure.
Key Characteristics of Hydrocarbon-Resistant Cables
Hydrocarbon-resistant cables are designed to endure challenging conditions that standard cables cannot handle. Here are some of their defining characteristics:
- High Chemical Resistance
These cables are chemically stable when exposed to various hydrocarbon-based substances, reducing the risk of breakdown or erosion over time. - Durability and Longevity
The materials used in hydrocarbon-resistant cables are known for their durability. They withstand both physical and chemical wear, making them ideal for long-term applications. - Thermal Stability
In environments where temperatures fluctuate, hydrocarbon-resistant cables remain stable. This is crucial in industries like oil extraction, where temperatures can be extreme.
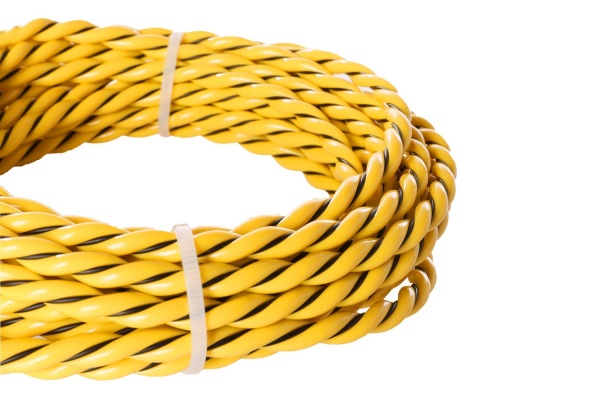
4. Fire Resistance
Some hydrocarbon-resistant cables are also flame-retardant, adding an additional layer of safety, particularly in environments where there is a risk of fires.
5. Flexibility
Despite their rugged nature, these cables maintain flexibility, allowing them to be installed in tight spaces or across complex industrial machinery layouts.
Manufacturing Standards and Certification
To ensure quality and safety, hydrocarbon-resistant cables must comply with industry standards and certifications. Oqo e oka kina na:
- IEC 60079-14 for explosive atmospheres
- ISO 14572 for cable resistance to chemicals and fuels
- UL standards, which include specific requirements for cables exposed to oils and hydrocarbons
These standards help to confirm the cable’s reliability and suitability for challenging environments.
Applications of Hydrocarbon-Resistant Cables
Hydrocarbon-resistant cables play an essential role in industries that operate in environments exposed to oil, gas, and other hydrocarbon-based substances. Here are some of the primary applications:
Oil and Gas Industry
The oil and gas sector heavily relies on hydrocarbon-resistant cables for drilling rigs, refineries, and distribution systems. They are used to control and power machinery, facilitate communication systems, and support monitoring equipment. These cables ensure smooth operations by reducing the risks of cable failure, which can result in costly downtime.
Chemical Manufacturing
Chemical plants deal with various hydrocarbons in their production processes. Hydrocarbon-resistant cables help ensure safe and reliable connections across machinery, providing essential protection against corrosive environments.
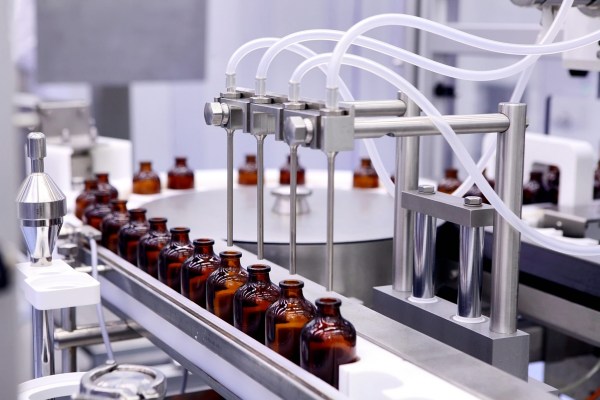
Marine and Offshore Applications
Offshore platforms and vessels face consistent exposure to hydrocarbons due to their proximity to oil extraction sites. Hydrocarbon-resistant cables used in marine environments support lighting, veisoliyaki kaukauwa, and data communication systems essential for safe and efficient operations.
Automotive Industry
In automotive manufacturing and repair facilities, hydrocarbon-resistant cables are critical. They are used in applications like fueling systems, lubrication processes, and power distribution within vehicles, ensuring safety and durability in fuel-exposed areas.
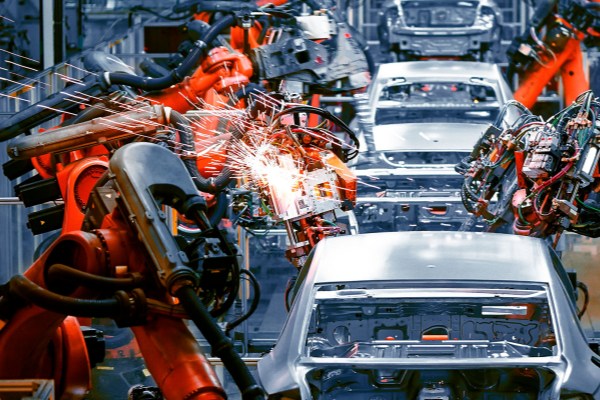
Mining Sector
Mines often have equipment exposed to hydrocarbons from fuel and lubrication systems. Hydrocarbon-resistant cables provide reliable power and communication solutions in these harsh conditions, minimizing the risk of equipment failure.
Industrial and Manufacturing Facilities
Many industrial settings use hydrocarbon-resistant cables for machinery that requires frequent oiling and lubrication. The cables ensure continuous operation of equipment by resisting oil exposure, which would otherwise compromise the performance of standard cables.
Railway and Public Transportation
The railway industry also benefits from hydrocarbon-resistant cables, especially in areas like fueling stations, maintenance hubs, and train construction. These cables support electrical systems, data transmission, and power delivery in environments where oil and fuel exposure is common.
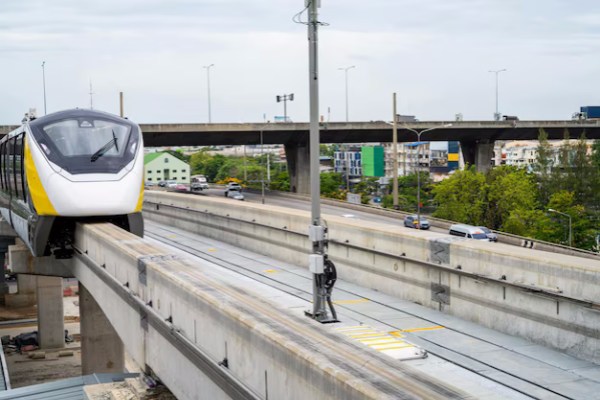
Choosing the Right Hydrocarbon-Resistant Cable
Selecting the appropriate hydrocarbon-resistant cable involves assessing factors like environmental conditions, cable material, and voltage requirements. Here are some steps to help in choosing the right cable:
- Assess Hydrocarbon Exposure
Determine the type and concentration of hydrocarbons present in the environment, as some materials are more suitable for specific hydrocarbons. - Consider Temperature Tolerance
Temperature resilience is essential if the cable will be used in an environment with extreme or fluctuating temperatures. - Check for Certifications
Look for cables that meet relevant industry certifications and standards, ensuring the cable’s suitability for the intended environment. - Evaluate Mechanical Requirements
Choose cables with suitable mechanical properties, such as flexibility, tensile strength, and abrasion resistance, depending on installation needs.
Installation and Maintenance of Hydrocarbon-Resistant Cables
Proper installation and regular maintenance are crucial for maximizing the lifespan and effectiveness of hydrocarbon-resistant cables. Some best practices include:
- Proper Cable Routing: Ensure cables are routed to avoid unnecessary bending or stress.
- Routine Inspections: Check cables for wear or degradation, as early detection can prevent larger issues.
- Scheduled Replacements: Depending on exposure levels and cable condition, consider scheduled replacements to avoid unexpected failures.
Hydrocarbon-resistant cables are indispensable in sectors where exposure to oils, fuels, and chemicals is inevitable. Their ability to withstand the corrosive effects of hydrocarbons makes them a preferred choice in the oil and gas, chemical, motoka, and marine industries, among others. By understanding their applications, standards, and maintenance needs, businesses can ensure safe and reliable operations in hydrocarbon-rich environments.