Abstract: Introduce the materials and structures of environmentally friendly mineral insulation fire cables, through designing mineral fire prevention insulating layers, thermosetting polymer protective layers, inorganic fiber filler, low smoke halogen-free silicon porcelain insulation layer, metal armor fireproof layer, fire prevention layer, and metal armor fireproof layer. The composite refractory structure is composed of low -smoke halogen-free environmental protection external care layer, realizing the environmental protection of cable fire resistance and low toxic environmental protection performance, low toxicity, and fire-resistant cable.
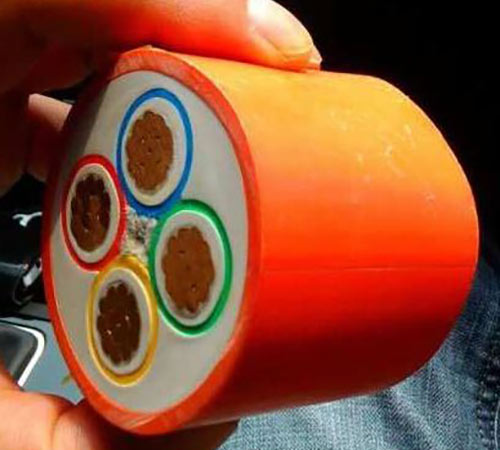
1 Introduction
With the formation of the three major metropolitan cities and national levels, the promotion of demand capacity policies, important engineering facilities, and high-rise buildings such as subways, power plants, nuclear power plants, roads, and high -rise buildings, smart communities, large supermarkets, public in the economy There are more and more people such as places and other people. The fire-tolerant cables required by these places not only have a general refractory function, because, in public places fire, but 80 % of the casualties are also caused by inhalation of a large amount of smoke or toxic gases when burning. And smoke is not conducive to the evacuation of personnel. Therefore, the cables on this occasion also require low smoke and halogen, high light transmission, and low toxicity. In view of the above site requirements and GB50217-2007 “Specifications for the Design of Power Engineering Cable“: Cable fire prevention and preventing extension regulations, environmentally friendly mineral insulation, and fire-resistant cables came into being. This article will introduce the structural analysis, material composition, manufacturing process, and related experiments of environmentally friendly mineral insulation fire cables, focusing on the production process of low smoke halogen-free silicon porcelain insulation layers and metal armor fireproof layers.
2 cable design
2.1 Structure analysis
The structure of environmentally friendly mineral insulation and fire-resistant cables is determined by the electrical performance, refractory performance, low -tobral halogen-free performance, and low toxicity required in the refractory environment. Polymer protective layer, inorganic fiber filling charging, low smoke without silicon porcelain insulation layer, metal armor fireproof layer, low smoke no environmental protection outer care layer, etc.
The conductor of environmentally friendly mineral insulation and fire-resistant cable adopts a tight -complicated circular conductor with a smooth surface, which is conducive to the tight wrap of mineral insulation and fireproof layer. It can reduce the oxygen content during burning. Because the mineral insulating fireproof layer is easy to absorb, the electrical performance is greatly reduced in a humid environment. In order to adapt to the humid environment, a layer of the high molecular protective layer is crowded on the mineral insulation prevention layer, which greatly enhances the environmentally friendly cable. Electrical performance and adaptability.
When the cable core forms a cable, the center fills the inorganic fiber filling rope and the subsequent squeezing low-smoke halogen-free silicon porcelain insulation layer, which is conducive to reducing the overall air content of the cable, which can significantly improve the flame retardant and refractory resistance of the cable.
The outer layer uses a chain armor fireproof layer and a low-smoke halogen-free environmentally friendly outer cover. While increasing the overall softness of the cable, it improves the low toxic performance of the environmentally friendly mineral insulating thermal cable.
2.2 Material composition
The structure of environmentally friendly mineral insulation fire cables is mainly by the copper conductor, mineral insulation fireproof layer, thermosetting polymer protective layer, inorganic fiber filler, low smoke halogen-free silicon porcelain insulation layer, metal armor fireproof layer, and low smoke without no smoke. Composition of halogen environmental protection external care layer, among which mineral insulation fireproof layers, inorganic fiber filling feasts, low smoke halogen-free silicon porcelain insulation layers, metal armor fireproof layers, low -tobacco -halogen-free environmental protection outer care layer constitutes the compound fire prevention of environmental protection cables Layer, the following mainly introduces the composite fireproof material composition.
(1) Mineral insulation fireproof layer: The inorganic mineral insulation layer adopts the synthetic Yunmu belt (fluorine Jinyun mother). The cloud mother belt is replaced by fluorine ion instead of hydrocarbon base, without crystalline water, the melting point is 1375 ° C, the safety of safety is large, and it has a natural Yunmu Bring. The characteristics: that is, small expansion coefficients, large dielectric strength, high resistance, and uniform dielectric constant, and also have the characteristics of high heat resistance level, which fully meets the requirements of (950C-1000 ° C), with a thickness range of 0.08-0.20mm The maximum supply width is 920mm, which can meet the daily ordinary equipment process requirements.
(2) Inorganic fiber filling: This filling has the characteristics of high-temperature resistance, super soft, lightweight, and high strength. It does not contain harmful substances such as halogen, asbestos, glass fibers, etc. Require
(3) Low -smoke-free silicon porcelain gum insulation layer: Low smoke-free silicon porcelain gum materials are based on silicon porcelain glue as the base material and carrier to add inorganic nano-silicon powder refractory filling, ceramic additives, and various additives to compound Success, after pinching and mixed, make a rubber that can be used for mold pressure or squeeze out. Among them, the silicon porcelain rubber matrix mainly provides the mechanical properties and process performance of composite materials. The burning ashes are used as the heat insulation refractory layer. The ashes and refractory fillers do not fall off during the combustion process. They still have a certain mechanical strength and promote the formation of the ceramic layer, and improve the mechanical strength and electrical insulation performance of the ceramic layer. Preparation and so on.
Ceramics silicon porcelain glue is the residual ashes formed by the high temperature when the fire occurs at the high temperature of the fire to form a layer of insulation and refractory ceramic layer with a certain mechanical strength. The electrical properties of the wire core ensure the normal work of the fire-resistant cable in a fire. The decomposition process of ceramic refractory silicon porcelain glue is as follows:
Low-smoke-free silicon porcelain tapestry is filled with squeezed molds to fill the material into the cable gap and uses a large amount of hydrolytic combustion-free flame-free material with a large number of hydrophobic oxides. Calories, reduce the temperature on the surface of the cable; the evaporation of the release of water molecules can also absorb a large amount of heat. The formed water vapor can bleak the concentration of oxygen around the cable. It reaches 3000 ° C. With the rise in temperature, it is quickly burned into a complete ceramic-shaped hard shell. The longer the ablation time, the higher the temperature, and the harder the shell, the harder and firm the shell.
Because the material has the effect of heat insulation, cooling, and shell after heating, the hard shell generated after burning is covered on the cable core, and the heat and heat are transmitted and spread inside the cable. Function, ensure the smooth flow of the line under fire conditions.
4) Armor: The armor layer adopts galvanized steel belt and double-layer chain around the bag. This form of armor can improve the overall softness of the cable, which is conducive to the laid and installation of the project site.
The armor layer can block the spread of flames to the internal spread of the cable, but it cannot be completely transmitted to the inside of the heatstroke in the inside. The purpose of fire prevention.
5) Outside condoms: Select the combustible flame-free material with hydrophilic oxides. It should have the effect of heat insulation, cooling, low smoke amount and low toxicity, and a high oxygen index.
Through mineral insulation fire prevention layers, inorganic fiber filling, low smoke-free silicon porcelain insulation layer, armor, and outer sleeve achieve the purpose of stabilizing and continuous power supply within a certain period of time under the flame conditions.
3. Manufacturing process and test
The product’s refractory environmental protection performance is determined by its composite fire protection structure. The following mainly introduces important processes of the fire-resistant composite structure.
(1) Conducting process: The conductor is the main carrier to ensure electrical performance. In order to ensure the requirements of the product’s electrical performance, the copper wire made of oxygen and copper pull should be used for twisted. Between 0.85-0.88, the surface is smooth, without burrs, and has sharp edges, which is conducive to the latter synthesizing the wound bag of Yunmu.
(2) Synthetic Yunmu Bandbing Bags: Different specifications of cables should choose the suitable width of the Yunmu belt. When the bag is wrapped in the scene, the tension is controlled. , Through folds, edges, and cloud -mother powder.
(3) Low smoke-free silicon porcelain gum insulation layer and outer cover crowded bag:
This material has a large viscosity and poor liquidity. During the production, a special screw with a low -scaling ratio must be used. In order to achieve the rounded effect, low-smoke halogen-free silicon porcelain tape insulation layers can be formed at one time when producing Fill in the wire core gap to ensure that the wire core is closely combined with the thermal insulation layer. In actual production, the speed and extrusion temperature of the screw should be controlled to prevent the fire performance of the heat insulation layer and the sheets due to excessive squeeze.
(4) Chain armor fireproof layer: Metal armor fireproof layer is produced in the form of spiral chain armor. In actual production, the angle and mold location of the guide board should be reasonably controlled. More than 15 °, the angle will make the chain armor folds reduce the overlapping rate width. When the on-site construction is bent, the metal chain armor is separated. When the mold is molded, the center hole of the mold must be aligned with the center position of the cable, and it is consistent with the level of the metal belt of the chain armor. Otherwise, when the armor belt runs at a high speed, the spiral armor belt is unevenly disconnected. With the phenomenon, the chain armor has lost its protective effect. With the structure of the spiral chain armor, the minimum curved radius of the cable can reach 7D (D is the outer diameter of the cable) during the actual engineering installation.
4 conclusion
Environmental-friendly mineral insulated fire-resistant cables through mineral insulation, inorganic fiber filler, low smoke halogen-free silicon porcelain insulation layer, metal armor fireproof layer, low smoke, and halogen-free environmental protection external care layer to form environmental -friendly cables compound It can pass the refractory test of BS7846: 2009, and it can also meet the requirements of smoke toxicity, corrosion resistance (pH value, conductivity) and tobacco density in GA306.2-2007, and achieve safety and environmental protection requirements.